A belt grinder is a tool that I wanted to have for a long time. For no particular reason. I’m not a knifemaker and I don’t do a ton of metal work so I could never justify the costs of buying one to myself. But what if it’s a project for a video? With that in mind, I started my design of the belt grinder.
For this project, I thought it would be nice to change things up a little bit and also dive into the design process a bit.
My goal for this project was to end up with an awesome powerful professional-style belt grinder but also to make it possible for others to make this belt grinder easily.
When making a design like this I first make my wishlist:
Tilting design
Small footprint
Possibility for later additions
Beefy motor
Simple to build
Usable for various materials
Having a list like this gives me a starting point for the design process. The small footprint made me decide to go with a 2x48” belt design and the wish for a beefy motor and suitable for various material made me decide to go with a 3 phase motor on a VFD. This way I can adjust the speed to the material I’m grinding.
The design process
I start my design process by selecting the parts that I already know I need and that have a large influence on the design. In this case the motor, the wheels, and the belt size. For all these parts I draw a simple model or I download the 3d file from the manufacturers’ website this way I can import them all in my CAD software and play with the arrangement of them until I’m happy about it.
When all the parts are arranged I start by designing the concept of the machine. Using simple blocks I make various arrangements until I’m satisfied with how it looks and works. Only when this is all done I start by going into more detail on the parts. I start adding holes for connections, nice fillets in the corners and everything else that is needed to make it a working machine.
Design considerations
On this belt grinder, I decided to make it mainly from sheet metal. Nowadays it is super easy to get sheet metal laser cut and delivered to your home so I figured this would be a nice way to make a design so others can replicate it without being a good welder.
The motor
I wanted a belt grinder that is STRONG, I don’t want to hassle with something underpowered when grinding metal. Doing my research I found that it’s recommended to have 1 HP for every inch of belt width. That meant for the two-inch belt I needed a 1.5kW motor since the price difference was only a little bit I decided not to fuzz around and I got the 2.2kW motor at 3000RPM. This motor is 3HP. It’s a beast!
To get variable speed control on the motor I bought a 3 Phase 230V motor which I’m connecting to a VFD. These motors can be wired in multiple ways; delta or star configuration. This configuration is how the power is distributed over the spools inside the motor. Wiring it wrong can cause the motor to instantly short out so check with your VFD and situation what you need.
In short, most motors are made with a 230/400V configuration. This means that the spools are made for 230V.
Star configuration: the voltage is shared between spools
Delta configuration: the voltage goes through one spool at a time (higher voltage per spool)
In my case having a 230V inverter, I need to wire the motor in Delta configuration to get all the power over the spool.
The belts
Different materials call for different belts and different belt speeds.
The harder the material to grind, the harder the belt material should be as well. Sounds easy, but there are a lot of options.
With all the choice I had no idea what I needed so I asked Jonathan from Multitoolproducts Europe. He gave me this advice:
In general, this is a good guideline:
For steels: Ceramic belts - Very good performance and sensibly priced.
For Aluminium: Zirconia - These also work reasonably well for mild steels
For wood: Aluminium Oxide - For general work Zirconia is fine also.
For deburring, blending and satin finishes go for Surface Conditioning Belts like Scotchbrite
Speeds
Not only the right belts are important for the material, but the right speed is also just as important to avoid burning the material instead of grinding it. These are some guidelines that I found and use:
Stainless steel, HSS - 20-30m/s
Carbon steel - 30 - 40m/s
Aluminium & soft metals - 20 - 30 m/s
Wood - 15 - 30m/s
Plastics - 5 - 15m/s
These are all speeds based on the belt speed. By multiplying the circumference of the drive wheel (in meters) to the rotations the motor makes per second you will get the belt speed. To be able to reach the higher belt speeds I chose a 5-inch drive wheel together with a 3000 RPM motor.
Machine specs
Motor: 2,2kW 3000 RPM
VFD: 2,2KW
Belt size: 2x48 inch
Belt surface speeds: 5 to 20 m/s
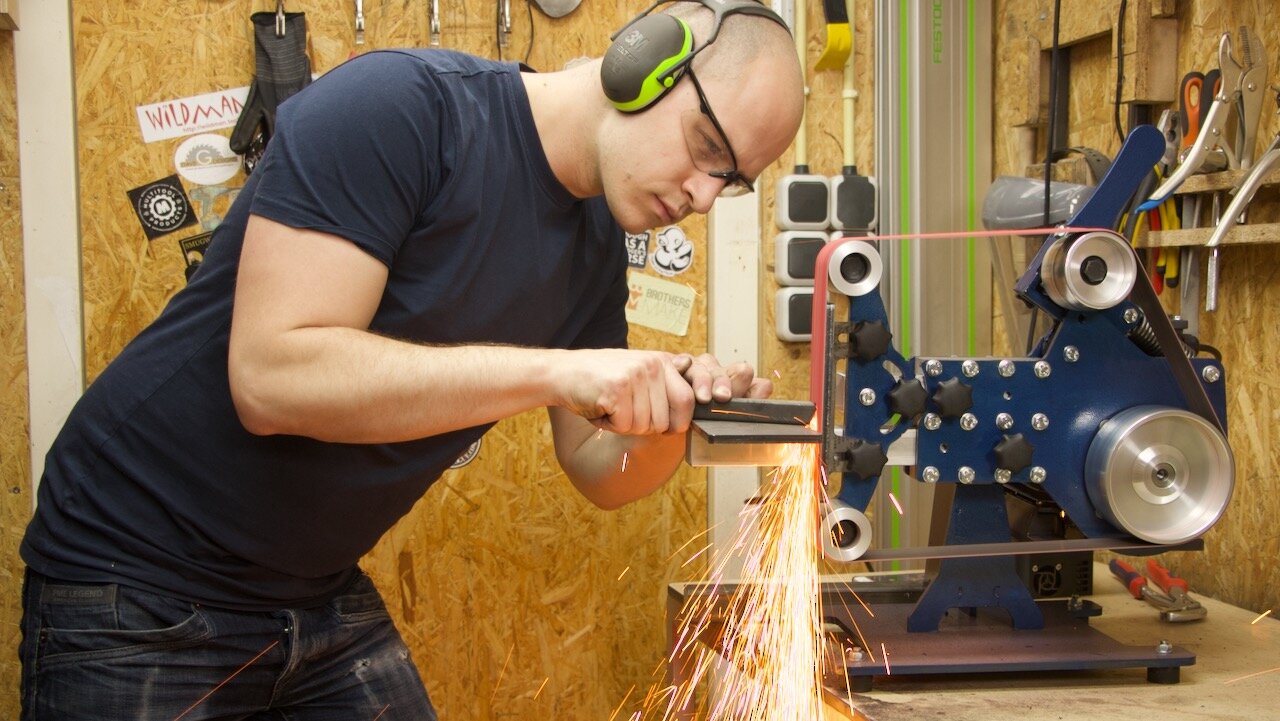
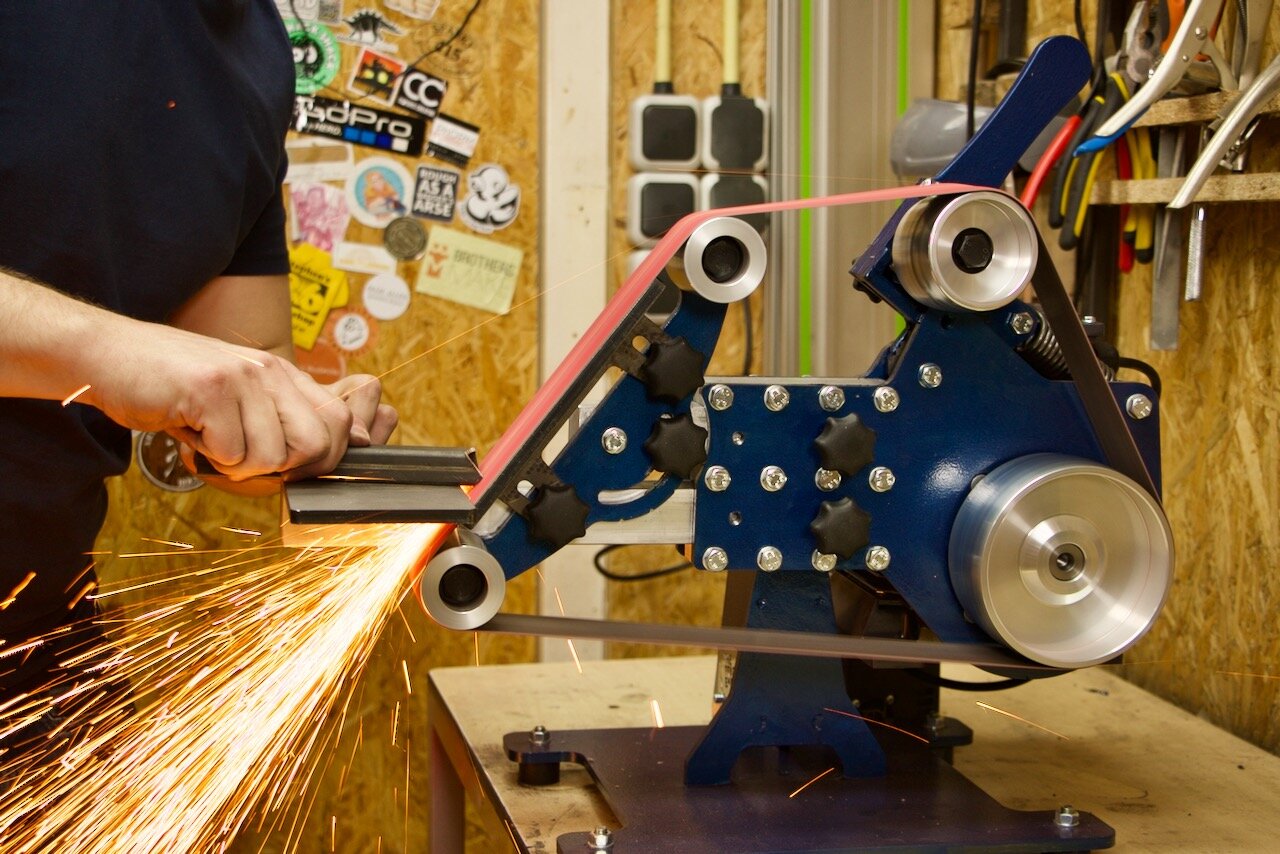
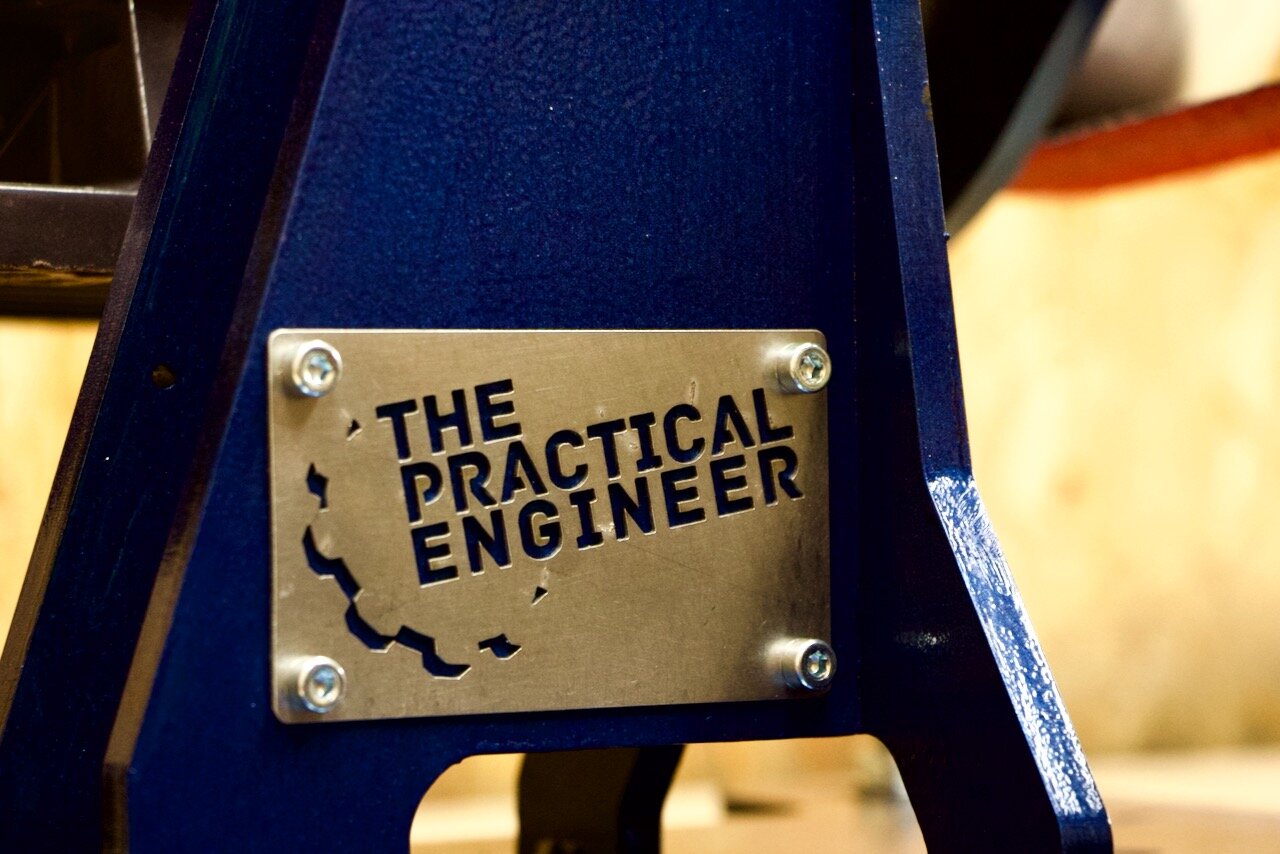
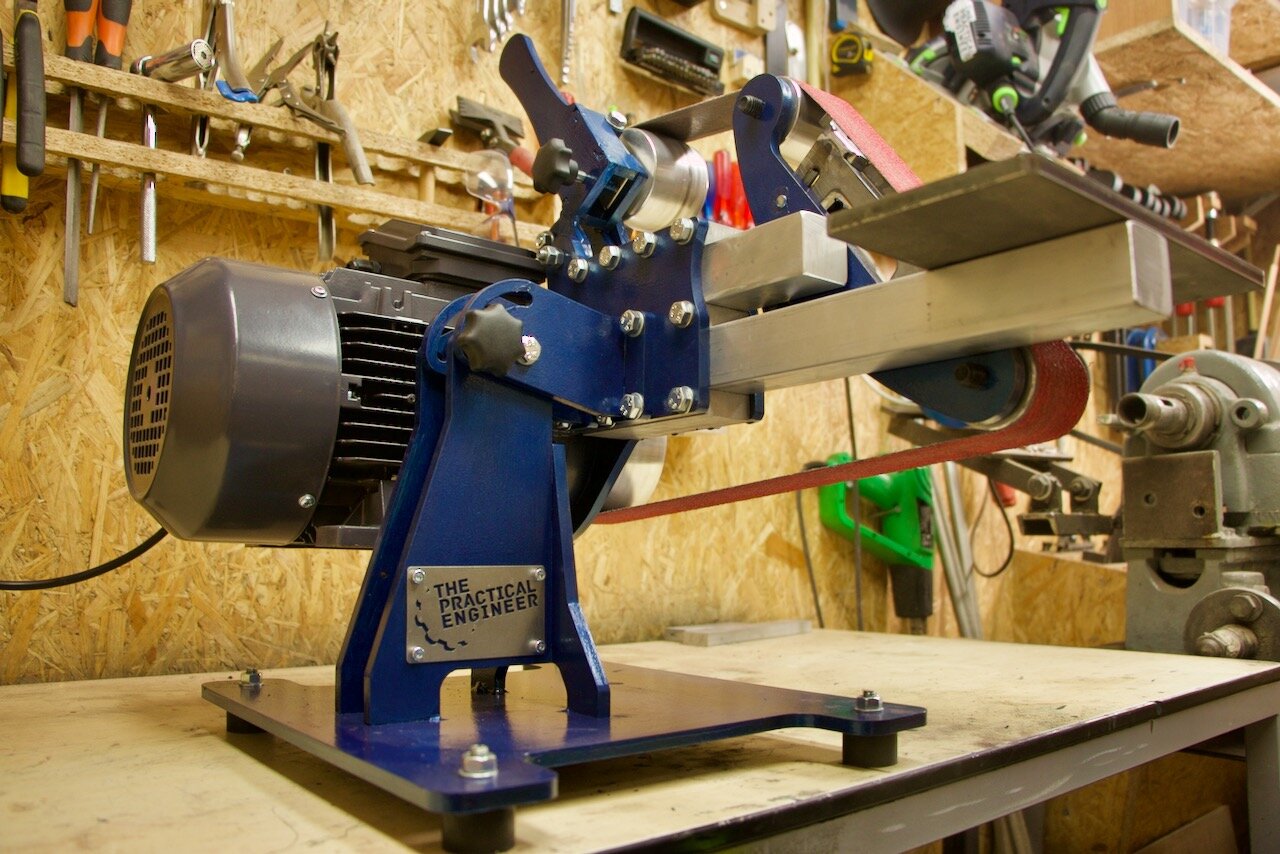
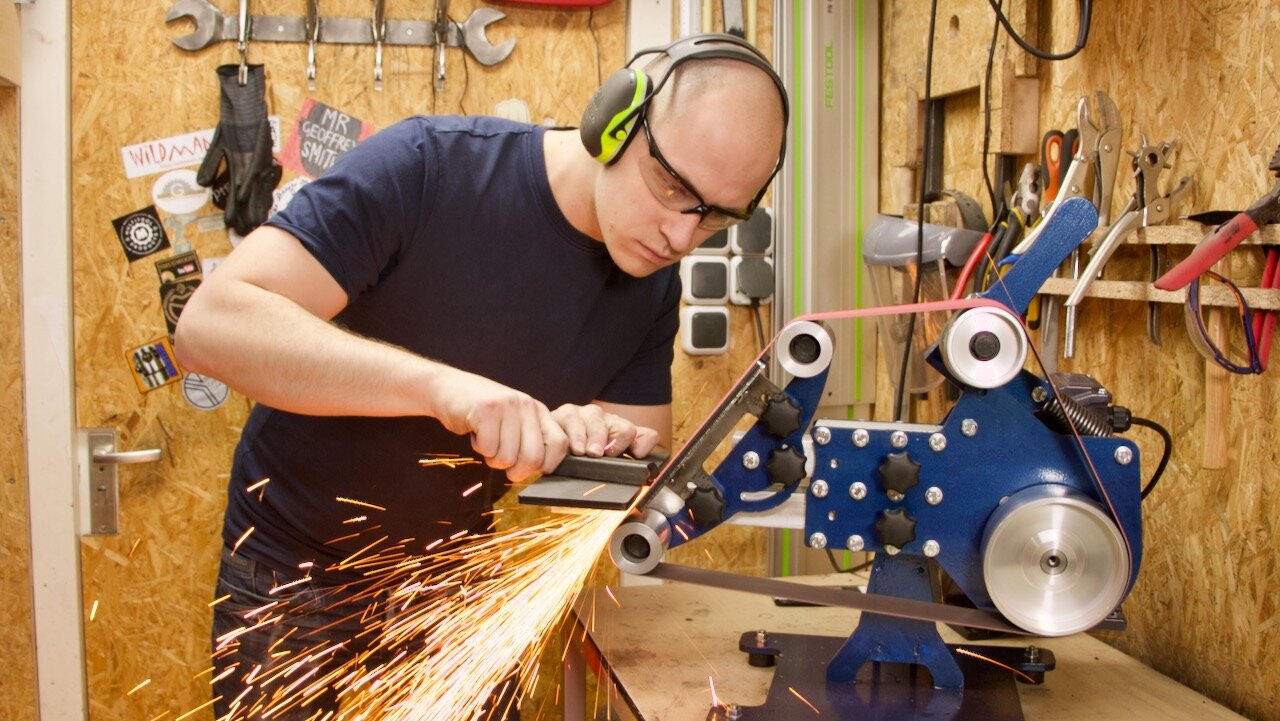
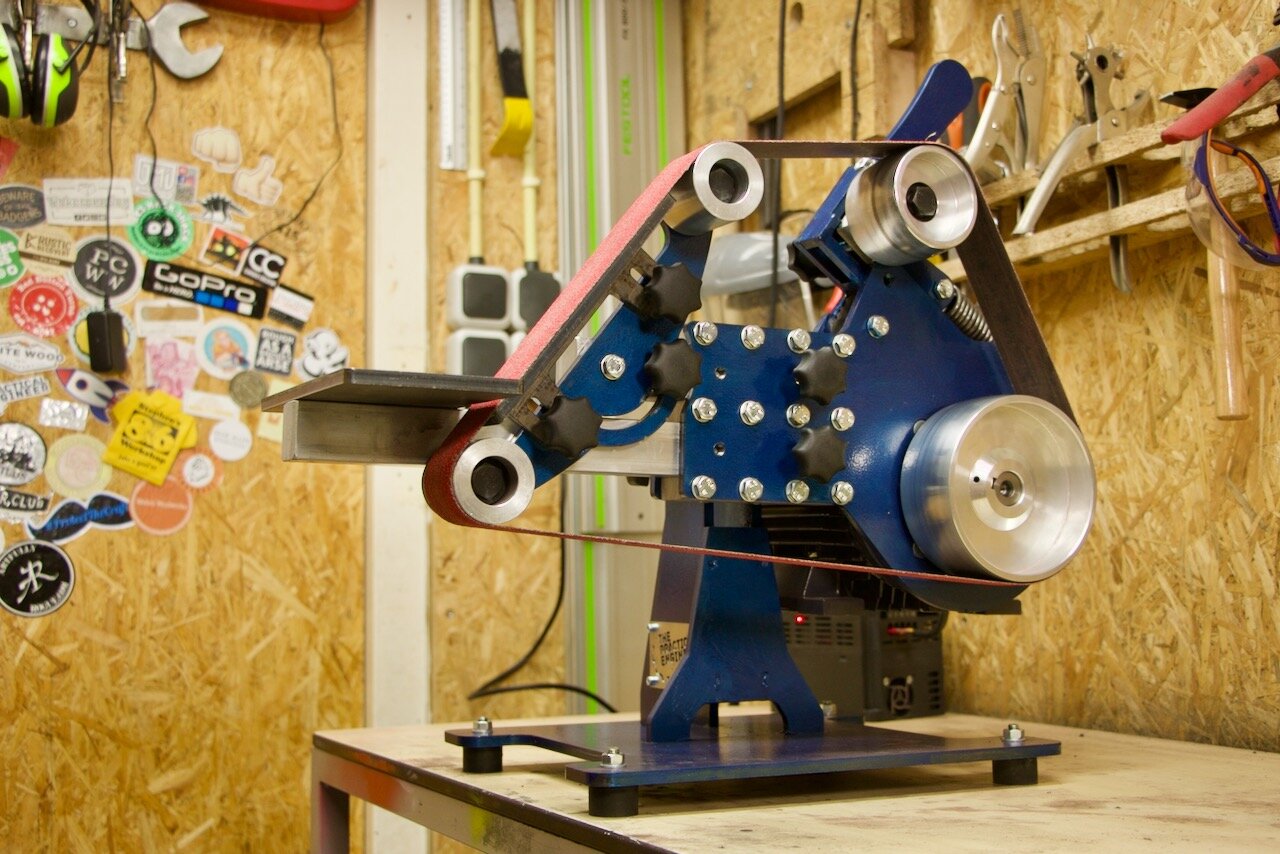
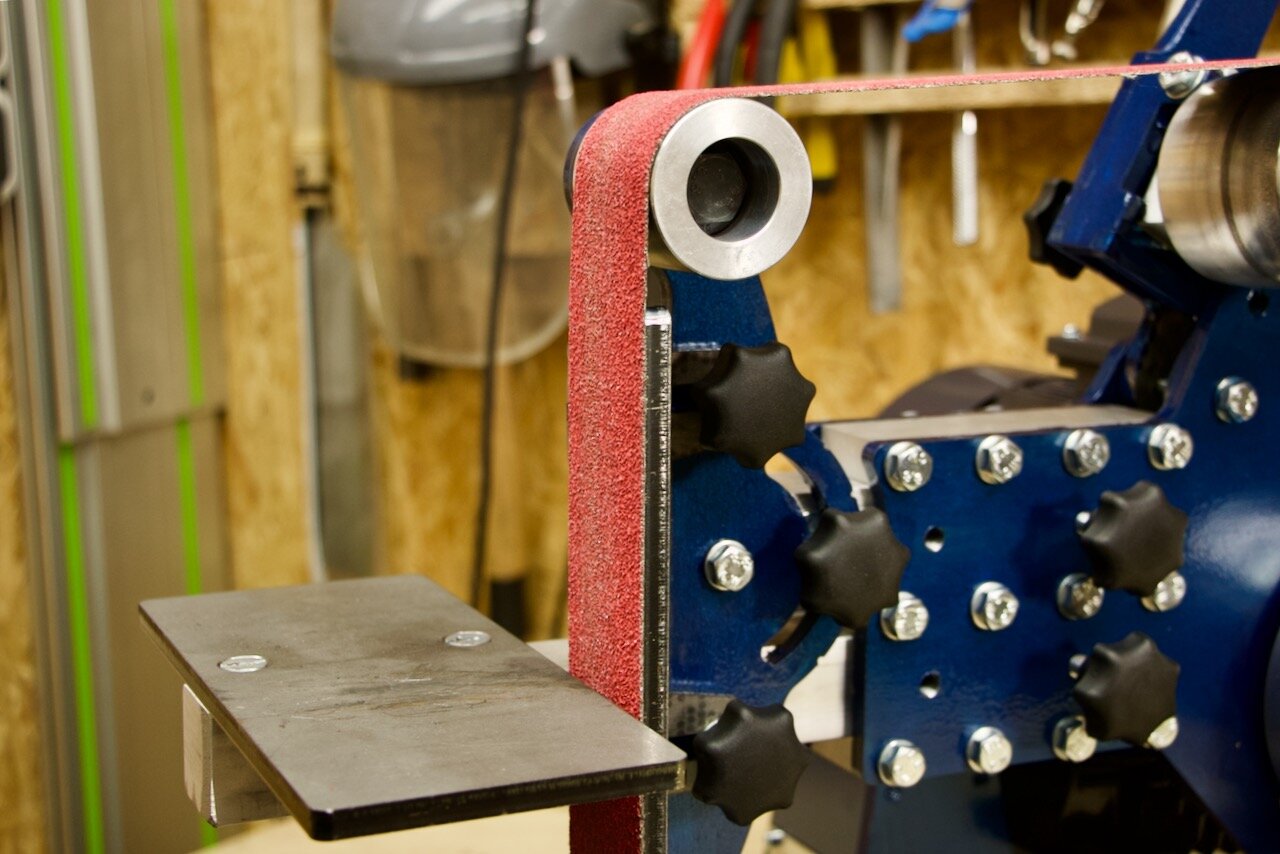